The air we breathe is made up of 78% Nitrogen, 21% Oxygen and 1% Argon, Water Vapor and Inert Gases. As a result of this composition, when nitrogen, water vapor and the inert gases are physically removed from the air stream, the remaining component in the air stream is oxygen. The air is said to be oxygen enriched, usually 90% to 99% oxygen content. This physical process of extracting the various components of air is known as "Air Separation". The process is environmentally clean and involves no chemical reactions of the air components being
separated. There are
basically two air separation technologies that are commonly
used in the industry; the distillation process and the
adsorption process.
The air distillation technology can
separate pure gases from air by first cooling the air until it
liquefies, then selectively distilling the components at their various boiling temperatures. The process can produce high purity gases but
it is bulky and energy-intensive. It requires that the temperature of the air stream be lowered through a highly complex refrigeration process to liquefaction.
This process separates atmospheric air into its primary components, typically nitrogen and oxygen, and
when required, argon and other rare inert gases.
The
adsorption process, on the other hand, is commercially used to
separate a single component from ordinary air at near ambient
conditions. It employs methods such as membrane technology, pressure swing adsorption
(PSA), vacuum swing adsorption (VSA) and vacuum pressure swing adsorption
(VPSA). Specifically, the PSA, VSA and VPSA technologies can
be used to produce 90% to 95% oxygen enriched atmosphere
typically required in medical oxygen therapy. These processes
are modular, with low energy consumption. They can be used to manufacture portable oxygen generating plants at various capacities from 10 cylinders per day to 200 cylinders per day.
|
|
PSA
Oxygen Production Process
Pressure
Swing Adsorption |
|
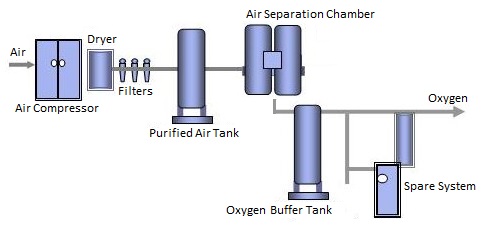
|
|
VSA Oxygen Production
Process
Vacuum Swing Adsorption |
|
Vacuum swing adsorption (VSA) segregates certain gases from a gaseous mixture at near ambient pressure; the process then swings to a vacuum to regenerate the adsorbent material.
VSA differs from other PSA techniques because it operates at near-ambient temperatures and pressures. VSA typically draws the gas through the separation process with a vacuum.
For oxygen and nitrogen VSA systems, the vacuum is typically generated by a blower. |
|
|
Pressure swing adsorption (PSA) is a technique used to separate some gas species from a mixture of gases (typically air) under pressure according to the species' molecular characteristics and affinity for an adsorbent material. It operates at near-ambient temperature.
Selective adsorbent materials, such as zeolites (molecular sieves), activated carbon, etc., are used as trapping material, preferentially adsorbing the target gas species at high pressure. The process then swings to low pressure to desorb the adsorbed gas.
Pressure swing adsorption process (PSA) is based on the phenomenon that under high pressure, gases tend to be trapped onto solid surfaces, i.e., to be "adsorbed". The higher the pressure, the more gas is adsorbed. When the pressure is dropped, the gas is released, or desorbed.
PSA can be used to separate gases in a mixture because different gases are adsorbed onto a given solid surface more or less strongly. For example, if a gas mixture such as air is passed under pressure through a vessel containing an adsorbent bed of zeolite that attracts nitrogen more strongly than oxygen, a fraction of nitrogen will stay in the bed, and the gas exiting the vessel will be richer in oxygen than the mixture entering.
When the bed reaches the limit of its capacity to adsorb nitrogen, it can be regenerated by decreasing the pressure, thus releasing the adsorbed nitrogen. It is then ready for another cycle of producing oxygen-enriched air.
Using two adsorbent vessels allows near-continuous production of the target gas. It also allows a pressure equalization, where the gas leaving the vessel being depressurized is used to partially pressurize the second vessel. This results in significant energy savings, and is a common industrial practice. |
|
|
VPSA Oxygen Production
Process
Hybrid Vacuum Pressure Swing Adsorption |
|
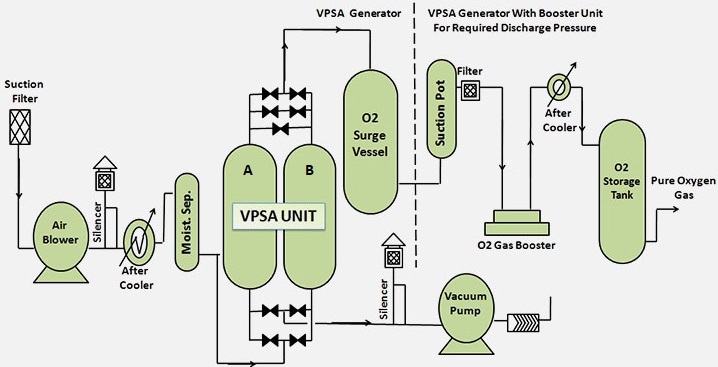
|
|
|
Hybrid Vacuum Pressure Swing Adsorption (VPSA) systems apply pressurized gas to the separation process and a vacuum to the purge gas.
VPSA systems, like one of the portable oxygen concentrators, are among the most efficient systems measured on customary industry indices, such as recovery (product gas out/product gas in) and productivity (product gas out/mass of sieve material).
Each adsorber undergoes a cyclic process, consisting of adsorption (O₂ production), desorption (evacuation) and re-pressurization (pressure build-up). The plant is often designed as
a “2-bed system”, such that when one bed is in the adsorption stage, the other is in the regeneration stage.
In the adsorption stage, vessel (A) is fed with compressed process air through an open-air valve. Moisture and carbon dioxide are captured at the entrance zone of the adsorber. Nitrogen molecules are continuously adsorbed, thus separating oxygen molecules from nitrogen molecules. At the discharge side of the adsorber, the dry oxygen flows into the buffer vessel. Before the adsorbent is fully saturated with nitrogen, the system switches over to the other bed in order to regenerate the saturated adsorber.
While the first adsorber is in adsorption stage, the second bed (B) is regenerated by opening the residual gas valve, which is connected to a vacuum pump. This pump draws out moisture, carbon dioxide and nitrogen in the opposite direction to the gas flow in adsorption mode. This residual gas is vented to the atmosphere.
The re-presurization stage is typically used to reduce energy consumption during the pressurization of the regenerated adsorber. Dry gas from the pressurized adsorber (A) flows to the evacuated adsorber (B). To increase pressure further, the process air blower pressurizes ambient air and feeds it into the adsorber (B). And so, the cycle continues.
Generally, higher recovery leads to a smaller compressor, blower, or other compressed gas or vacuum source and lower power consumption. Higher productivity leads to smaller sieve beds. |
|
|
|
Partnership
& Business Model
| Technology
| Plant Specifications
| Containerized
Solutions |
|
<< Return
to Products & Services |
|
For more information, Contact
Us |
|